A Review on Pyroprocessing Techniques for Selected Wastes ...
Generally on cement mills, the product is ground dry in a ball mill. It has a relatively wider particle size distribution; hence, it is required to operate the ball mill in a closed circuit with a size classifier with an efficient or sharp cut of the size separator. ... "Comparison of the overall circuit performance in the cement industry ...
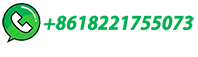