Milling Media - Ball Mill - Grinding Media - Grinding ...
The Perfect Grind Starts with the Perfect Grinding Media. Whatever you are grinding, in a ball mill or bead mill, you'll find the right grinding beads for the job, here at FOX.. What applications can you use FOX Grinding Media for? From Albania to Zimbabwe, and everywhere in between, FOX grinding beads are used as milling media for the ultrafine grinding of Coatings, Paints, …
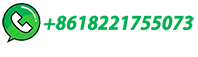