Grinding Media - 911Metallurgist
Effect of Ball Size and Properties on Mill Grinding Capacity Current ball milling theory suggests that grinding capacity is influenced by the size of balls charged to the mill. In selecting the appropriate ball charge, the first objective is to determine that ball size which will grind the coarse particles most efficiently. This size should be the largest ball size charged to the mill. The ...
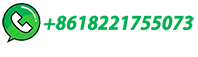