Studies Show Snags to Mill Optimization | E & MJ
Studies Show Snags to Mill Optimization. More than 100 virtual operators have been deployed over the course of three years at Los Bronces mine. Above, the Los Bronces mine milling control room in Chile. (Photo: Anglo American) Two studies identify obstacles to SDGs, while a major miner announces the windfall from deploying automation.
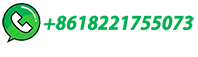