Module-5.pdf - GRINDING PROCESS V.Gunasegaran Assistant ...
Grinding Process Grinding is a surface finishing operation where very thin layer of material is removed in the form of dust particles. Thickness of material removed is in range of V.Gunasegaran, Assistant Professor, Department of Mechanical Engineering, BSACIST, Chennai - 48 0.25 to 0.50 mm. Tool used is a abrasive wheel Grinding machine is a ...
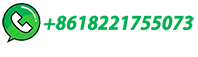