Laboratory Ball Mills, Planetary Ball Mill, High Energy ...
The grinding balls in the grinding jars are subjected to superimposed rotational movements, the so-called Coriolis forces. The difference in speeds between the balls and grinding jars produces an interaction between frictional and impact forces, which releases high dynamic energies.
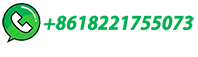