3M Superabrasive Wheels for Cutting Tools
2 3M™ Superabrasive Products for Manufacturing Cutting Tools 3M™ Superabrasive Wheels for Cutting Tools Glossary The following is a brief description of terms for the most common round tool grinding applications: Cut-Off Using a thin wheel to trim blanks to length.
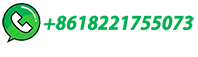