(PDF) A techincal report on design of hot oil system
A general process flow diagram of hot oil system commonly employed in oil and gas plants ... Contaminates can also includ e dirt, sand, dust, mill . ... (bar/100m) Suction ≤ 2 0.6 0 ...
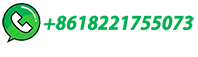
A general process flow diagram of hot oil system commonly employed in oil and gas plants ... Contaminates can also includ e dirt, sand, dust, mill . ... (bar/100m) Suction ≤ 2 0.6 0 ...
Purchasing & Procurement Process Flow Chart. Edit this example. Customer Payment Process Flow. Edit this example. Medical Services Flowchart ... Vendor Payment Process Chart. Edit this example. Ordering Services Process Flowchart. Edit this example. Late Payments Process Map. Edit this example. Audit Flowchart. Edit this example. DIN 66001 ...
Complete process flow chart. Click and press to drag the flow chart. Where there is this icon you can view the process video. download a PDF file in A3 format. Scroll down. Steel making. Hot working. Cold working.
Good figures for rod and bar mills are 90 % to 93 %, for structural mills, the good mill utilization figures are 75 % to 78 %. If a mill rolls …
Rolling is a process of reduction of the cross-sectional area or shaping a metal piece through the deformation caused by a pair of rotating in opposite directions metal rolls. 4 The gap between the rotating rolls is less than the thickness of the entering bar therefore a friction force is necessary in order to bite the bar and to pull it ...
Production Process. Check the seamless steel pipe and welded steel pipe (ERW/LSAW/SSAW) production process flow charts of below, steel plate and steel coil production process flow chart is also shown here!
The process is continuously repeated as the particles move by mass and volume action through the mill. ... the feed trunnion is smaller than the discharge trunnion to ensure a good flow and no backflow to the feed. Diagram of ball mill and interior cut away [image: (135-7 …
In all ore dressing and milling Operations, including flotation, cyanidation, gravity concentration, and amalgamation, the Working Principle is to crush and grind, often with rob mill or ball mill, the ore in order to liberate the minerals. In the chemical and process industries, grinding is an important step in preparing raw materials for subsequent treatment.
Ikea Production Process Flow Chart. lisya on November 18, 2021. The Primary Sector The primary sector involves the development of the raw materials. The designer then sends the brief to IKEAs staff designers and freelancers and refines promising designs until settling on the one to produce. Ikea Chart Creately.
Wood received at a pulp mill may be in several different forms, depending on the pulping process and the origin of the raw material. It maybe received as bolts (short logs) of roundwood with the bark still attached, as chips about the size of a half-dollar that may have been produced from sawmill or veneer mill waste or pre-chipped from ...
Interactive Steel Manufacturing Process AIST's Making, Shaping and Treating of Steel ® Wheel. AIST has collaborated with Purdue University Northwest's Center for Innovation Through Visualization and Simulation to create a unique, interactive experience of the steel manufacturing process. This one-of-a-kind experience allows you to click on each phase of …
The manufacturing process of TMT Bar involves series of processes like rolling, water quenching, heat treatment, cooling at various stages of manufacturing. The Thermo Mechanical Treatment involves 3 essential steps that are: Quenching. Self Tempering. Atmospheric cooling. The quality of TMT Bar depends on three major factors.
The roughing mill is made up of Multiple independent rolling mill stands, Billets heated in the furnace until they glow bright orange-yellow are rolled through one stand at a time to produce transfer bars suitable for finish rolling. High-pressure water-jet nozzles clean the oxidized iron, or scale, from the surface along the way.
Forming the 7 basic tools of the quality control process is a process flow diagram. Flowcharts make it easy to understand the product or service process, outline quality control, and increase efficiency. You could try EdrawMax and build the quality control process with flowcharts that deliver results. Flowchart made simple clearly illustrates ...
Special Bar Mill: Structural Mill . Steel Melt Shop & Continuous Casting: Steel is made in steel melting shop in the refractory lined vessels called LD Converters by blowing oxygen through the hot metal bath. While iron making is a reduction process, steel making is an oxidation process. The oxygen reacts with impurities like carbon, silicon ...
papermaking process. Figure 1: Process Flow Diagram of the Papermaking Process Introduction. Stock preparation is the interface between the pulp mill/warehouse and the paper machine . Pulp Mill. Raw stock. Stock Preparation. Paper Machine. Finished stock Objectives. Treat and modify the raw material stock. Finished stock meets the requirements ...
The bar mill produces straight bars of 18–120 mm in diameter and bars in coil of 18–52 mm in diameter. After shipment from the mill, these straight bars and/or bars in coil are processed to end products (fasteners, shafts, hubs, cranks, and so on) which are char-acteristically used as machine parts after various processing steps,
The bar mill produces straight bars of 18–120 mm in diameter and bars in coil of 18–52 mm in diameter. After shipment from the mill, these straight bars and/or bars in coil are processed to end products (fasteners, shafts, hubs, cranks, and so on) which are char-acteristically used as machine parts after various processing steps,
In the continuous casting process the molten metal is poured directly into a casting machine to produce billets, with a cross section 165mm2. 3 Hot rolling and thermo mechanical treatment. A Quenching. When a hot rolled bar leaves the final mill stand (including roughing mill, intermediate mill, finishing mill, etc.), it is instantaneously ...
• rolling mill • standard operating practices in rolling mill • manufacturing process • process flow chart • suppliers of plant and equipments • complete indian suppliers of plant and machinery for re-bars • suppliers of raw materials. appendix – a : 1. cost of plant economics 2.
Ioc Ball Mill Process Flow From Ethiopia . 11.7.2 Process Description13-5 Figure 11.7-1 presents a general process flow diagram for ceramic products manufacturing. The basic steps include raw material procurement beneficiation mixing forming green machining drying presinter thermal processing glazing firing. Get Price
Please note: This diagram aims to show steelmaking today. This diagram does not feature the new input materials and processes that are being developed and will dramatically change how we make steel in the next 30 years as we transition to the low carbon economy.
MANUFACTURING PROCESS There are six basic processes in the manufacture of tires: 1. Mixing of carbon blacks, elastomers and chemicals in the "Banbury Mixer" to form the rubber compounds. 2. Calendering the fabrics and steel cord and coating them with rubber.
Resistant to Corrosion: The TMT process gives these bars anti-corrosive properties. These bars undergo controlled water-cooling process that resists formation of coarse carbides. Coarse carbides are the main reasons for the corrosive nature of a common bar. Absence of surface stresses is another reason for these bars to be corrosion resistant.
Sawmilling lumber is a throughput process where a raw or rough log starts a journey through mechanized steps and emerges as a smooth finished product. Modern sawmills operate as an on-demand, pull-through system with the mechanized mill parts sitting between the front end loggers and the tail end marketplace.
the relevant process variables with special computation models and thus determines the optimum stand size for the particular layout. With HL mill stands, plant owners achieve optimum results in bar steel mills, wire rod mills, light section mills and combination plants. MAIN FEATURES OF THE HL DESIGN C, riid dei e r Lo r edi avre ri
Electric Arc Furnace Steelmaking Process. 1. Feeding. The operation of adding molten iron or scrap steel to the electric furnace is the first step of the electric furnace steelmaking operation. 2. Slagging. The operation of adjusting the slag composition, alkalinity, viscosity and reaction ability in steel and iron production.
What Is A Rolling Mill? In metalworking, rolling is a metal forming process in which metal stock is passed through one or more pairs of rolls to reduce the thickness and to make the thickness uniform. The concept is similar to the rolling of dough. Rolling is classified according to the temperature of the metal rolled.
Mannesmann Plug Mill Pipe Manufacturing Process. Mannesmann was a German engineer who has invented this pipe manufacturing process. The only difference between the Plug mill process and the Mandrel mill process is that in the mandrel method inside diameter is achieved in a single pass whereas in Mannesmann multi-stage reduction is possible.
Rod mills are used in an open circuit between crushing and the ball mill. They often operate in wet and where the pulp contains up to 50% solid by mass. This machine is equally very applicable to dry where it could take a feed that has achieved 6% moisture. As such, when the product is sticky, rod mills are preferred over ball mills.
حقوق النشر © 2024.Artom كل الحقوق محفوظة.خريطة الموقع