grinding principle in cement industry
Grinding trends in the cement industry Cement Lime Gypsum 4/1/2010 Summary: The main trends concerning grinding processes in the cement industry are still hi +86 21 33901608 [email protected] Home
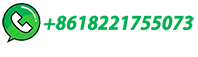
Grinding trends in the cement industry Cement Lime Gypsum 4/1/2010 Summary: The main trends concerning grinding processes in the cement industry are still hi +86 21 33901608 [email protected] Home
Traditional clinker grinding station adopts ball mill to grind clinker, and has much dust, loud noise and high energy consumption in the process of production, it will be replaced gradually by vertical roller mill. Great Wall Machinery is the professional manufacturer of cement equipment, can offer complete solution for grinding station, and improves production efficiency, reduces …
The UAE is now home to 12 integrated cement plants, eight cement grinding plants and 17 cement producing companies (Figure 2). The integrated cement plants have 29Mt/yr of cement production capacity, while the cement grinding plants have 10.44Mt/yr of capacity, giving a total of 39.84Mt/yr. Almost half, 13.3Mt/yr or 45.9%, of the UAE's ...
Kudithini Cement Grinding Plant inaugurated in Karnataka on January 4, 2010 with a capacity of 1.1 MTPA of Portland Slag Cement. ACC acquires 100 percent of the financial equity of Encore Cements & Additives Private Limited which is a slag grinding plant in Vishakhapatnam in coastal Andhra Pradesh.
Cement Grinding Plant Price - Select 2021 high quality Cement Grinding Plant Price products in best price from certified Chinese Cement Production Plant manufacturers, Cement Mixing Plant suppliers, wholesalers and factory on Made-in-China
Cement industry committed to construction culture; ... Our experienced specialists regularly implement optimisation projects for industrial grinding plants in the cement industry and associated branches throughout the world and are fully familiar with the requirements of industrial practice. Within the framework of individual projects and in ...
Generally cement plants are fixed where the quarry of limestone is near bye. This saves the extra fuel cost and makes cement somehow economical. Raw materials are extracted from the quarry and by means of conveyor belt material is transported to the cement plant. There are also various other raw materials used for cement manufacturing.
16 Tomorrow's cement plant 18 Service Individual requirements, optimal solutions thyssenkrupp Industrial Solutions is the cement industry's competent technology partner. As one of the few international full-line cement plant manufacturers we offer you sophisticated and innovative plant solutions based on more than 150 years
1.5 Finish Grinding ... account for 30 to 40 percent of the industry's cash costs. While current energy ... of cement plants as well as to a larger range of stakeholders. Michel Folliet Chief Industry Specialist Cement, Manufacturing, Agriculture and Services Milagros Rivas Saiz
Qiziliqumsement prepares to launch Kiln Line 4. 18 November 2021. Uzbek cement producer Qiziliqumsement has invested US$112m to add a fourth production line. This is the company's the first significant investment in the plant since 1989 and it is due to come on-stream in December. Qiziliqumsement's new line, located just outside Navoi, will ...
improve cost effectiveness. Cement FingerPrint ensures tuning of plant control system efficiently, benchmarked to Industry-best practices. Further, Cement FingerPrint offers a systematic approach in capturing the process sensitivity using plant step tests, building a dynamic process model, analyzing
UNISOL INC (UNISOL) is a provider of cement additives, grinding aids and construction chemicals catering to the custom needs of cement and construction industry. Our products and services are targeted at enhancing cost and quality competitiveness of our clients. Our expertise lies in offering global sourcing of specialty chemicals, in-depth ...
Cement plants > 1.0 million. tonnes/annum. production capacity <1.0 million tonnes/annum production capacity. All Stand alone grinding units. General Condition shall apply. Note: 1. Fuel for cement industry may be coal, petcoke, mixture of coal and petcoke and co-processing of waste provided it meets the emission standards. 2.
Mini Cement Plant Features. Cement plants with clinker capacity between 50tpd and 1000tpd can be called mini cement plants or small cement plants.Mini cement plants are very popular among small and medium-scale cement manufacturing enterprises since they do not require very large cement production capacities.
To reduce transportation costs, the layout of cement production is to build a cement clinker production line in the mining area and establish a cement grinding plant near the cement sales market. If the clinker production line is built near the city, for every 1t of clinker produced, about 1.6t of cement raw material is needed, and the ...
Calculation of Cost for 1m3 of Concrete. Let's consider the concrete mix of M15 (1:1.5:3), where, 1 is the part of cement, 1.5 is the part of fine aggregates and 3 is the part of coarse aggregates of maximum size of 20mm. The water-cement ratio required for mixing of concrete is taken as 0.45. 1. Assumptions:
In Cement Plant, the wear resistant material of liners, grinding media, Crusher Hammer, Jaw Plates, Cheek Plates, etc. are widely used in different kinds of machines in the cement production process. ... In Construction Aggregate Industry, Crushers are widely used, and in order to reduce the cost, Resminer can provide you wear resistant ...
The initial review discusses new cement plant construction cost and offers a cost estimate for four typical plant sizes which have been recently studied by the ... Cement industry news from Global Cement. 9 Jan 2013 … Liberia currently has …
India: Naveen Patnaik, the chief minister of Odisha, has attended the inauguration of Ramco Cement's new cement grinding plant at Haridaspur. The unit had a cost of just under US$100m and has created 105 direct jobs. A LM 46.2+2 CS type vertical roller mill with a capacity of 3750kW has ordered from Germany-based Loesche in 2018 for the project.
Therefore, Clinker Grinding Unit system has simple technology, low failure rate, high operation efficiency, compact allocation, construction area of 70% of ball mill, construction space of 50-60% of ball mill, and it can help enterprises to save land resources effectively. 3. With excellent environmental benefit, low noise, and low dust.
According to MoEF sources proposal is to expand the existing capacity of 2.4 MTPA to 3.6 MTPA Cement Grinding Unit, and establishing 2×18 MW Coal/ Pet Coke based Captive Power Plant. The existing plant of 2.4 MTPA is under construction and likely to be completed by FY16-17 . Cost: The estimated cost of the project is Rs 400 Crores.
Abstract: A Cement plant is an energy intensive industry both in terms of thermal and electrical energy and more than 40% of production cost is accounted for by the cost of energy. With intense competition in the market place on price, energy conservation offers itself as a low cost option to cut costs and create a market edge.
2 Conditions during the cement grinding process 3 Demands of standards and construction industry 1 The characteristics of the local raw materials, the availability of pos-sible clinker replacements and the conditions during the cement grinding process are different in every individual cement plant. In addition the
St Marys Cement grinding plants at Badger, Wisconsin and Detroit can also produce up to 350,000 MT of slag annually. Just-in-time model assures efficiency, helps control costs The St Marys distribution network relies on an intricate network of barges operating on the Great Lakes as well as rail cars and trucks moving throughout the region, Jim ...
The cement grinding plant cost depends on changing factors like scale, location, labor, raw materials, etc. Therefore, it's impossible to nail down a perfectly accurate, one-size-fits-all answer. As cement grinding plant manufacturer, we'd like to lower customers' cost with cheaper and more reliable cement machines.
The U.S. cement industry is made up of either Portland cement plants that produce clinker and grind it to make finished cement, or clinker-grinding plants that intergrind clinker obtained elsewhere, with various additives. Clinker is produced through a controlled high-temperature burn in a kiln of a measured
The site selection of a cement factory is very important. A good site can make construction easier, save construction costs and subsequent production costs. Since the coverage area of a cement plant is very large and the cement industry produces heavy pollution, cement plants are usually built in the urban periphery or rural areas.
Feeling the heat: Reducing the environmental cost of manufacturing, construction in Northland 9 Dec, 2021 04:00 PM 8 minutes to read Golden Bay Cement is New Zealand's only fully integrated cement ...
The grinding plant at a cement factory is used to reduce the particle size distribution of various materials such as raw meal, fuel or clinker to set parameters. In a sense, a grinding plant uses energy (through milling) to create fineness …
Clinker Grinding Units : - Ashoka Group supplies a cement grinding unit with each of its cement plant. Grinding units can also be supplied separately for other cement plants. We supply grinding units upto 2000 TPD plants, capable of handling all types of cement.
حقوق النشر © 2024.Artom كل الحقوق محفوظة.خريطة الموقع