Mini-Mill PULVERISETTE 23 / Description - fritsch.de
The FRITSCH Mini-Mill PULVERISETTE 23 grinds the sample through impact and friction between grinding balls and the inside wall of the grinding bowl. For this, the grinding bowl performs vertically oscillating movements with 900 – 3,000 oscillations per minute at 9 mm amplitude. In contrast to similar mills, a clearly better degree of ...
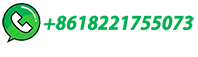