Ball Milling | Material Milling, Jet Milling | AVEKA
The optimal milling occurs at a critical speed. Ball mills can operate in either a wet or dry state. While milling without any added liquid is commonplace, adding water or other liquids can produce the finest particles and provide a ready-to-use dispersion at the same time.
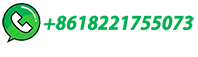