Grinding Wheels Types, Material & Specifications ...
It specifies the upper and lower limits at the certain points in the size distribution. The various grit size systems are ANSI-bonded, FEPA-F, JIS, and Micron Graded. Applications. Grinding wheel specification depends on these aspects such as. Material Removal, Intermediate Cut And Finish, Finishing Cutting, Corner Holding, Cleaning ...
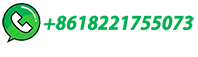