(PDF) INVESTIGATION OF EFFECTS OF GRINDING MEDIA …
There are many factors which effect grinding performance of ball mills like; liner design, speed, charge ratio, grinding media distribution, grinding …
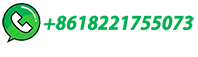
There are many factors which effect grinding performance of ball mills like; liner design, speed, charge ratio, grinding media distribution, grinding …
Factors Affecting Ball Mill Grinding Efficiency. 25/10/2017 The following are factors that have been investigated and applied in conventional ball milling in order to maximize grinding efficiency: a) Mill Geometry and Speed – Bond (1954) observed grinding efficiency to be a function of ball mill diameter, and established empirical relationships for recommended media …
The objective of this dissertation was to investigate how media shape affects grinding. Ball size distribution inside an industrial mill was analysed in terms of shapes and sizes. Load behaviour, mill power and breakage as affected by media shapes were studied in a pilot laboratory mill. An inductive proximity probe, light
evolution of grinding models which incorporate liberation as a parameter (Andrews and Mika; 1976, Peterson and Herbst; 1985, Choi 1986). — A n. With the existing size reduction models, much work has been done_in studying the effect of operating parameters such as mill speed and ball loading on model parameters and
Ball mill grinding efficiency is influenced by many factors: ore grindability, feed size, grinding product size, ball mill diameter and length, ball mill working speed, liner type, steel ball loading system, grinding concentration, return sand ratio in closed-circuit grinding and feed rate. (Ball mill) To improve the ball mill grinding efficiency, you must first understand the …
Ball mill: When the particle size of the product is less than 0.5mm, the grinding effect of the ball mill is greater than that of a rod mill of the same specification. SAG mill: The SAG mill has a wide range of feeding particle sizes and can process larger minerals, but at the same time, its output particle size is relatively larger.
Alumina ceramic grinding balls are made from materials such as bauxite, roller powder, industrial alumina powder, high-temperature calcined Alpha alumina powder, etc., through batching, grinding, powdering, molding, drying, firing and other processes., Mainly as a grinding medium Quality and widely used ball stone. Alumina ceramic grinding balls have …
Ball joints are an important suspension component found on virtually all modern vehicles. They are a spherical bearing in a socket — functioning similarly to the ball and socket design of a human hip — and serve as one of the main suspension pivot points connecting the control arms of the vehicle to the steering knuckles.
Ball milling pretreatment of corn stover for enhancing the efficiency ... Meanwhile, the results indicate that the treatment effect of wet milling is better than that of dry milling. The optimum parameters for the milling process were ball speed of ... number of balls of 20 (steel ball, Φ = 10 mm), grinding for 30 min. Get Price.
The grinding efficiency of ball milling is greatly affected by the jar rotation speed, ball size, and ratio of balls and sample talc [22,24,25]. A faster rotation speed generally produces talc with a smaller particle size and lower …
However, this problem is difficult to solve because there are too many parameters that affect the size of the grinding ball. At the current cognitive level of human, it is impossible to deduce the theoretical calculation formula of the milling ball diameter. This is because it is impossible to include more than a dozen factors that affect the ...
The ball millliner and grinding medium are directly contacting with the ore particles which affects the movement state of the grinding media and the ore particles and affects the grinding effect. Among the influence of the ball mill lining on the grinding effect the most important one is the influence of the material and the liner's shape on grinding effect.
Competitive landscape : Leading companies in the Chrome Alloy Cast Grinding Balls Market are Magotteaux, TOYO Grinding Ball, Jinan Xinte, Dongyuan Steel Ball, Jinan Huafu, Jinchi Steel Ball... Chrome Alloy Cast Grinding Balls Market 2021 : Global Industry Analysis, Driving Factors, Trends, Market Size and Forecasts Up to 2027 with Dominant ...
Methods of operating ball grinding mills – W. R. Grace & Co. … to the mill charge, adding chemicals affecting the … ball grinding mills and … as the rate of …
When charging a ball mill, ceramic lined mill, pebble mill, jar mill or laboratory jar use on a jar rolling mill it is important to have the correct amount of media and correct amount of product. Charging a Wet Mill – The general operation of a grinding mill is to have the product impacted between the balls as they tumble.
For example, Turner (1979) has demonstrated an overall increase in capacity of almost 800 percent by ball addition to an ore of extreme difficulty to …
As for the dry grinding method, the moisture of raw material can affect ball mill capacity and quality. The higher the moisture content of the milled material will cause saturated or greasy so that the capacity and quality of ball grinding machinewill be reduced.
During the grinding process, coarser material (size class 1) break to finer material (size class 2) and (size class 3) which are termed the daughter products, as shown in Fig. 1.A chemical reaction on the other hand can consist of say reactant 'A' forming intermediate product 'B' then proceeding to final product 'C' or a competing reactant 'A' to final product 'D' can also ...
In practice, several parameters affect the performance of ore grinding processes. Accordingly, using a laboratory scale ball mill, the influence on energy efficiency of some of these parameters ...
Superfine grinding by ball milling for 24 h can thus be used to produce superfine QSL powder with higher free phenolic metabolite content and antioxidant activity, and improved water solubility index, color, bulk, and tapped densities. This study will be useful for the food / …
plant ball mill's grinding efficiency (Fig. 1). The functional performance parameters "mill grinding rate through the size of interest," and "cumulative mill grinding rates" from both plant and small-scale tests are applied to this task. A plant media sizing methodology, and industrial case studies, are provided. Background
8.1 Grinding 8.1.1 Grinding action Industrial grinding machines used in the mineral processing industries are mostly of the tumbling mill type. These mills exist in a variety of types - rod, ball, pebble autogenous and semi-autogenous. The grinding action is induced by relative motion between the particles of media - the rods, balls or pebbles ...
5. Refill steel ball accurately. Obviously,the grinding action between steel ball and ore causes the wear of steel balls, which can change the …
The breakage and liberation of minerals are the key to fluidized mining for minerals. In the ball milling process, steel balls function as …
The grinding efficiency is reflected in the processing capacity of the mill and the fineness of the grinding ore. Large diameter steel ball help reduces grinding time thus improves grinding efficiency, in addition, putting some small steel ball to control the particle fineness effectively. In fact, the steel balls are continuously worn and the ...
Ball Mills For Sale South Africa What Affect The BallMill Grinding Efficiency. There are many factors that can influence of ball grinding process, it mainly includes the following three aspects:. TECHNICAL NOTES 8 GRINDING R. P. King - Mineral Technologies ...
INFLUENCE OF AN ORGANIC POLYMER IN BALL-MILL GRINDING OF QUARTZ, DOLOMITE, AND COPPER ORE By A. R. Rule, 1 A. J. Fergus,2 and C. B. Daellenbach 3 ABSTRACT Research was done by the Bureau of Mines to determine the effect of a
The following are factors that have been investigated and applied in conventional ball milling in order to maximize grinding efficiency: a) Mill Geometry and Speed – Bond (1954) observed grinding efficiency to be a function of ball …
Grinding medium of ball mill 1 High manganese steel. It has high toughness, good manufacturability and low price. The surface layer of high manganese steel will harden rapidly under the action of great impact or contact. The harder index is five to seven times higher than other materials, and the wear resistance is greatly improved. ...
Ball milling Grinding Energy consumption abstract The influence of several grinding parameters such as charged material volume, ball filling ratio, and mill rotation speed on energy efficiency of fine...
حقوق النشر © 2024.Artom كل الحقوق محفوظة.خريطة الموقع