Circuit Drawings and Wiring Diagrams
Line diagram: a one-line diagram or single-line diagram is a simplified notation for representing an electrical system. The one-line diagram is similar to a block diagram except that electrical elements such as switches, circuit breakers, transformers, and capacitors are shown by standardized schematic symbols. Figure 3—One-line diagram
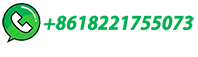