Mesoporous silicon nanoparticles covered with PEG ...
Silicon nanoparticles (SiNPs) prepared by mechanical grinding of luminescent porous silicon were coated with a biopolymer (dextran) and investigated as a potential theranostic agent for bioimaging ...
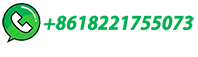