Method for producing extrafine pure metal powder - GTE ...
We claim: 1. A method of producing extrafine pure elemental metal powder from a starting material consisting of a highly malleable pure elemental metal powder, comprising the steps of: oxidizing said highly malleable pure elemental metal powder, grinding the resulting oxide, reducing the ground oxide in a reducing atmosphere to obtain a pure elemental metal …
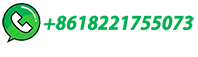