Coal Mining and Production - MIGA
Parameter Surface mining (t/1000t coal produced) Underground mining (t/1000t coal produced) Mining Techniques Contour Area Conventional Longwall Liquid effluents 0.24 1.2 1 1.6 Solid waste 10 10 3 5 Dust 0.1 0.06 0.006 0.01 Source: Based on Edgar, 1983 * (Note: Local conditions will form the basis for choosing the appropriate mining method) ...
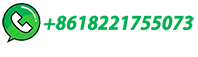