Wet FGD System Overview and Operation - WPCA
and ball mill operation • 16-24 hr capacity • Carbon steel construction with polymer or stainless steel hopper lining • Vibrating bottom/mechanical activation • Vent filter for fugitive dust control WPCA Wet FGD Seminar - December 1, 2008
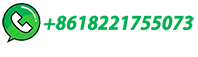