Ball Mill Heat Balance Explanation
The Art Of Sharing and...Imagination. Home; About Us; Services. Grinding Software; Consultancy; Training Courses; Calculators Online
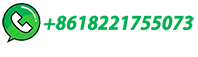
The Art Of Sharing and...Imagination. Home; About Us; Services. Grinding Software; Consultancy; Training Courses; Calculators Online
To determine the total heat loss from fin, we use the Fourier's Law at the base of the fin 0 x fin x T x q Ak (28) Figure 10. Under steady conditions, heat transfer from the exposed surfaces of the fin is equal to heat conduction to the fin at the base.
11.6 Portland Cement Manufacturing 11.6.1 Process Description1-7 Portland cement is a fine powder, gray or white in color, that consists of a mixture of hydraulic cement materials comprising primarily calcium silicates, aluminates and aluminoferrites. More than 30 raw materials are known to be used in the manufacture of portland cement, and these
Cement mill Admix mill Cement Silo Mixer Weigher Shipping Bulk loader Packer Marketing Packing center Packer tanker truckFreight car ship Cement Silos. ... (m3N/kg-cl) by heat balance method 2. Laos 2006.10 16 Air Leakage Measurement pre-kiln cooler heater raw mill EP cooling air combustion air fuel stack O2 O2 O2 O2 F possible air leakage
Calcination kinetics of cement raw meals under various CO 2 concentrations . J. R. Fernandez, S. Turrado and J. C. Abanades, React.Chem. Eng., 2019, 4, 2129 DOI: 10.1039/C9RE00361D This article is licensed under a Creative Commons Attribution 3.0 Unported Licence. You can use material from this article in other publications without …
World Cement mill only, and 10.8 kWh/t for the mill department at power meter (including mill, bucket elevators, ... ensuring the optimal thermal balance of ... as the hot gas generator is the only heat source and the corresponding fuel consumption is a critical operational cost. Moreover the absence of water injection in the mill has another ...
The Cement Formulae Handbook (Version 2.0) is an outcome of the excellent response & feedback to the earlier handbook (2009). I would sincerely request all the readers to not only make full use of the handbook across your organizations but also to pass any comments / suggestions / feedback on Cement Formulae Handbook (Version 2.0)
2.1 Heat Balance 01 In the process of clinkerisation, it is seen, that around 55% of the total heat input, is only utilised for clinkerisation. Waste gases account for around 35% of total heat input. Heat balance (per kg. of clinker) for a typical cement plant, is depicted in Table - 1: 5-Stage Preheater 6-Stage Preheater
Our all online and onsite training programs are designed with six-sigma and lean manufacturing theme for CCR Operators, Process Engineers quality peoples and plant technical management team. Learners can work alone, either in the office or at home, wherever a computer with an internet connection is available.
Heat loss distribution across different elements can be established through heat balance and process audit of pyro section. Fuels used commonly to provide heat for the conversion processes are coal, fuel oil, and natural gas. Alternative fuels like petcoke, rubber tyres, wood chips, etc. have been introduced to economize cement making process.
ºC * (100 – 19) ºC) + 539.0 kcal/kg * 0.85] qw = 599534 kcal/h Since more heat is given up by the cement than is absorbed by the water, air circulation through the mill must have helped cool the cement down to discharge temperature. 7.3 Heat Balance for Mill Cooling: In the following example, heat balances for mill cooling are calculated in ...
raw mill kiln storage bin cement mill storage bin dispatch Raw meal ESP Clinker Cement gas ... • Partial oxidation for heat supply CH 4 + ½ O ... (approximately 1000 balance spaces) balance spaces. Schematic diagram of the clinker burning process (reference) raw mill
Heat Quantity ... 4.3.1 Integrated Steel Mills ... Gases in Cement Kilns 36 Process Exhaust Gases in the Iron and Steel Industry 37 Table 13 Typical Coke Oven Gas Composition 38 Table 14 Basic Oxygen Furnace Offgas Composition 40 Iron/Steel Production 42
heat balance of cement plant – Gold Ore Crusher. Heat balance of the cement ball mill … unburnts in residue 1.0 % 12.7 % Fuel 100 % Steam Boiler 73.8 % Heat in Steam 8.1 % Example-2: Mass Balance in a Cement Plant. »More detailed
Mill Heat Balance. Critical Importance with respect to One Industrial Case Study. Lecture 10-. Ball Mill Internals Inspection. Ball Loading and Material Filling Measurements, Chamber Sampling Measurements, Circuit Samples, Implications. Lecture 11-. Industrial Case Studies. Raw Mill, OPC Cement Mill, PPC Cement Mill, Bauxite Mill Optimisation ...
Heat balance excel sheet - detailed calculations. Sharing is caring: here is my contribution to cement engineers community.An excel sheet (MS excel 2003) that can does heat balance for pyro section of cement industry.This sheet is …
balance over the kiln where the energy for calcination, drying as well as the heat energy of the in- and outgoing streams is accounted for. To calculate the heat energy of the different streams, polynomials were used to describe the temperature dependent heat capacities of the different components. The polynomials were fitted
The cooling of cement is an important step prior to storage in mitigating gypsum dehydration and subsequent moisture liberation which can lead to lump formation. Recommendations vary but it is generally accepted that with mill outlet temperatures of around 110ºC – 120ºC, cooling to below 80ºC is necessary to avoid this reaction.
Optimization of cement grinding using standard bond grinding calculations based on population balance models is successfully applied [4, 38]. Various grinding laws, energy relationships, control factors and controller design for cement grinding are discussed in [37]. Figure-1. Vertical roller mill for cement grinding [13].
Fig. 4, Fig. 5 show the heat versus temperature of the preheater bypass gases and the bypass dust, respectively. Fig. 5 shows incremental increases in gas heat of approximately 1%for every 5 K temperature increase through the series of cyclones. Fig. 6 shows that the dust heat content increases by 0.9% for every 5 K increase in temperature.. Download …
Announcement Welcome to the Cement Process October 1st, 2020. We encourage cement professionals Read more. Announcement October 1st, 2020. Excel Tools, PPT's, KAIZENS, MIP;s and many more
example mechanical energy to heat energy, but overall the quantities must balance. 4.2 The Sankey Diagram and its Use The Sankey diagram is very useful tool to represent an entire input and output energy flow in any energy equipment or system such as boiler, fired heaters, fur-naces after carrying out energy balance calculation. This diagram ...
MASS AND HEAT BALANCE. Please send me an excel sheet of heat and mass balance of cement mill (ball mill). Reply. Know the answer to this question? Join the community and register for a free guest account to post a reply. Page 1 of 1 1.
From the above pie chart, it is evident that the cement mill section (37%) is the major contributor to overall SEC, followed by kiln section (26%) and then by Raw mill section (22%), while all the other sections of the plant ... Overall Kiln Heat Balance The kiln and grate cooler heat balance is based on the above input baseline parameters ...
Kiln Operation. Pioneer Cement 22-28 July 2006. Prepared by Hatsachai prahanph Siam cement (Ta-Luang) Co.,ltd Training for Pioneer Cement Operation. Content Quality of Clinker Kiln Operation Parameter Cooler Operation Burner Operation. Training for Pioneer Cement Operation Clinker quality Clinker Component SiO2 22.8% Al2O35.98% Fe2O3 3.42% CaO 63.95%. …
1/12/2012 heat balance of cement plant – Gold Ore Crusher. Heat balance of the cement ball mill unburnts in residue 1.0 % 12.7 % Fuel 100 % Steam Boiler 73.8 % Heat in Steam 8.1 % Example-2: Mass Balance in a Cement Plant. »More detailed.
heat balance sheet for cement grinding unit. calculation of heat generated from grinding in, the grinding unit and is, To perform computerized mass …
A mill heat balance is one option to calculate the dosage … The best control regime is to monitor the cement from the mill in real time with XRD and use water … » More detailed Heat Balance Calculation in Cement Plant Sustainable Cement … Apr 13, 2011 · Heat Balance Calculation in Cement Plant document sample. Shared by: fjm15005. …
Heat balance calculators The calculation of the thermical balance of the ball mill is now proposed according 2 methods The first method, we know the ventilation of the mill the cement temperature and we want to calculate the water quantity we need to inject in order to get the temperature at mill outlet we would like to have. Get Price
Where a concrete floor slab is adjacent to the mill foundations, an expansion joint should be used. For convenience in maintenance, the mill foundations should be equipped with jacking piers. These will allow the lifting of one end of the mill by use of jacks in the event maintenance must be carried out under these conditions.
حقوق النشر © 2024.Artom كل الحقوق محفوظة.خريطة الموقع