What is Cement ball mill? - Quora
Ordinary cement ball mill is in general used in circuit grinding system. Its characteristics are high grinding efficiency, yield, low energy consumption, especially when grinding slag cement, its performance is more prominent. Usually output of cement ball mill can be increased by 15-20%, and power consumption is reduced by about 10%.
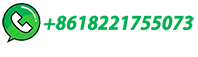