Milling formulas and definitions - Coromant
The milling process – definitions Cutting speed,v c Indicates the surface speed at which the cutting edge machines the workpiece. Effective or true cutting speed, v e Indicates the surface speed at the effective diameter (DC ap).This value is necessary for determining the true cutting data at the actual depth of cut (a p).This is a particularly important value when using round …
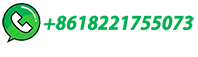