Ball Mills - Mineral Processing & Metallurgy
Nowadays grinding mills are almost extensively used for comminution of materials ranging from 5 mm to 40 mm (3/16″—1 5/8″) down to varying product sizes. They have vast applications within different branches of industry such as for example the ore dressing, cement, lime, porcelain and chemical industries and can be designed for continuous ...
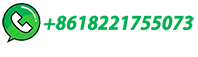