Cement | Minerals | AMETEK Land
Cement. Cement is manufactured through a closely-controlled chemical combination of calcium, silicon, aluminium, iron and other ingredients. Temperature monitoring at key stages is essential to providing this close control. Monitoring is also important to control emissions, ensure consistent quality, oversee the condition of the kiln, and ...
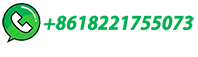