8 Principles of Centerless Grinding - Metal Cutting ...
Coolant is used in centerless grinding to not only keep the grinding wheel cool, but also remove heat from the zone where the workpiece contacts the grinding wheel. Centerless grinding requires the use of correctly pressurized coolant to overcome the air barrier created between the grinding wheel and workpiece during the grinding process.
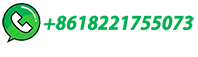