Ball Mills - Mineral Processing & Metallurgy
In these cases, the feed to the ball mill may be from 10 to 100 mesh or even finer. Here this Ball Mill Design Calculator.
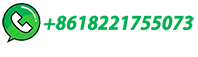
In these cases, the feed to the ball mill may be from 10 to 100 mesh or even finer. Here this Ball Mill Design Calculator.
To construct a design simulation model for a ball mill [1, 2, 3] which can be used to predict optimum ball mixture, it is necessary to know not only the effect on breakage of different ball mixtures, but also the equilibrium ball mixture in the mill. For wet ball mills, the equilibrium size distribution of balls in the mill is a function of the ...
The correct determination of the grinding balls bulk weight in mill allows accurately determination the mill balls feed weight. The mill balls feed weight is necessary for calculating the grinding media specific consumption and avoid mill overloading, thereby eliminating the motor load increasing possibility.
Retsch™ PM 400 Model Planetary Ball Mills meet all technical requirements for colloidal grinding and provide the energy input necessary for mechanical alloying. PM 400 is a robust floor model with 4 grinding stations. Brand: RETSCH 20.535.0001. Additional Details : Weight : 290.00000kg. Product Code. 10708981.
8.3.2.2 Ball mills. The ball mill is a tumbling mill that uses steel balls as the grinding media. The length of the cylindrical shell is usually 1–1.5 times the shell diameter ( Figure 8.11). The feed can be dry, with less than 3% moisture to minimize ball …
The above mix proportion is ground in Raw mill at 110 – 118TPH (Ball mill) to achieve desired fineness and fed into CF silo (continuous Flow silo – concreted, capacity 4500MTs) where extraction and filling takes place simultaneously. This kind of system is well-proven for uniform feed to kiln to avoid the variation in burning system. Soiled ...
The objective of feed mixing is to start with a certain assortment of ingredients called a "formula", totalling some definite weight. This is processed so that each small unit of the whole, either a mouthful or a day's feeding, is the same proportion as the original formula.
Milling Step-over Distance Calculator. In many milling operations, the cutting tool must step over and make several adjacent cuts to complete machining a feature. As a result, a small cusp of material, called a scallop, will remain between these cuts on any surrounding walls or on the machined surface if a ball end mill is used.
The maximum power draw in ball mill is when ball bed is 35-40 % by volume in whole empty mill volume. Considering that ball bed has a porosity of 40 %, the actual ball volume is considered to be ...
Ball mill: Ball mills are the most widely used one. Rod mill: The rod mill has the highest efficiency when the feed size is <30mm and the discharge size is about 3mm with uniform particle size and light overcrushing phenomenon. SAG mill: When the weight of the SAG mill is more than 75%, the output is high and the energy consumption is low ...
Ball mill is a type of grinder machine which uses steel ball as grinding medium, can crush and grind the materials to 35 mesh or finer, adopted in open or close circuit. The feed materials can be dry or wet, they are broken by the force of …
mills with the rod mill and ball mill laboratory work indices. Note, in Figure. 1, that the rod mill product slope is less than 0.5 due to an extra amount of nes present being fi fi ner than 650 μm. These fi nes proceed to the ball mill improving the ball mill effi ciency. Also, the plotted rod mill P80 value, as shown in Figure 1, is 2900 ...
The SMC™ test, stored in the "DWT" testwork table (SMC is a Drop Weight Test). Bond ball mill work index. The method requires all the parameters of the ball mill work index test to be filled in: Ball mill Wi test closing screen size, umclosing, µm; Ball mill Wi test product size, P 80, µm; Ball mill Wi test feed size, F 80, µm
Answer: Introduction of new Raymond mill Compared with the traditional mill, the new Raymond mill can meet the grinding requirements of dolomite, marble, limestone, barite, talc, gypsum and other mineral powder projects. It can produce powder fineness between 80-400 mesh, mill equipment covers a ...
Unlike the ball mill which utilizes a large number of hardened steel balls to impart the grinding action, the rod mill uses steel rods lying within the drum and parallel to its axis. When the drum rotates, these rods roll around inside it, thereby crushing the feed material between them.
Ball Nose End Mills. Ball nose mills have a radius at the bottom which makes for a nicer surface finish in your workpiece, meaning less work for you as the piece won't need to be finished any further. They are used for contour milling, shallow slotting, pocketing and contouring applications.
F80 is the milling circuit feed 80% passing size, µm, fSAG is a calibration parameter for pebble crushing and/or fine feed (typically 1.0 for 80% passing six inch mill feed and when no pebble crusher is present). WiBM is the Bond ball mill work index, unitless CFnet is an empirical adjustment to a ball mill circuit [CFnet = 2.35 - 0.29 × ln(P80)]
- Ball top size (bond formula): calculation of the top size grinding media (balls or cylpebs):-Modification of the Ball Charge: This calculator analyses the granulometry of the material inside the mill and proposes a modification of the ball charge in order to improve the mill efficiency:
Pulp samples collected around the ball mill or rod mill and hydrocyclones, screen or classifier (classification system) are screened and the cumulative weight percentage retained is calculated for several mesh sizes to obtain the Ball Mill Circulating Load. The percentage through the smallest mesh can also be used to determine Rcl, as follows:
Ball Mills Mineral Processing Metallurgy. Types of Mill Feed Chute Scoop Feeders for BallRod Mills are made in various radius sizes Standard scoops are made of cast iron and for the 3′ size a 13″ or 19″ feeder is supplied for the 4′ size a 30″ or 36″ for the 5′ a 36″ or 42″ and for the 6′ a 42″ or 48″ feeder. Get Price.
Ball charge management and maintenance. l10.6 x w2.5 x h2.8m. Total weight: approx. 6,800 kg with feeding hopper. The Magotteaux drum ball sorter consists of a ball hopper, a vibrating feeder with variable feed rate, a drum sorting system and eight exit chutes. The ball sorter allows for sorting balls of either the first or second compartment.
Ball Mill Working Principle. To be chosen according to the grinding material, material is composed of a ball mill feed end of the hollow shaft is arranged in the tube body, when the ball mill cylinder rotation time, grinding body due to inertia and centrifugal force, the effects of friction, making it attached to the cylinder liner on the cylinder body away, when taken to the height of a ...
High Energy Ball Mill E max the revolution in ultrafine grinding. High Energy Ball Mill E. The Emax is an entirely new type of ball mill for high energy milling. The unique combination of high friction and impact results in extremely fine particles within the shortest amount of time.
Ball mills give a controlled final grind and produce flotation feed of a uniform size. Ball mills tumble iron or steel balls with the ore. The balls are initially 5–10 cm diameter but gradually wear away as grinding of the ore proceeds. The feed to ball mills (dry basis) is typically 75 vol.-% ore and 25% steel. Get Price
High-efficiency milling is based on the "radial chip thinning" theory that's been around for a long time. The basic idea is to keep the tool cutting at an ideal chip load. To increase the metal removal rate, the stepover is substantially reduced from the typical 50% of tool diameter, but the feed rate is increased in order to maintain the ...
The weight of steel balls in the ball mill is between 1.5-338t. There are two types: dry and wet grinding methods. are the hot-sale models, whose capacity is 3.5-6t/h, 8-43t/h, 65-248t/h. we can recommend the best model for you according to your requirement. Small, medium and large-sized models are in stock now. Get the latest price list. 1.
(24.8 lb) of ball mill feed sample from plant survey. Sample is reconstituted with water to be the same percent solids as the plant ball mill discharge. Mill speed: 35.2 rpm (65 percent of critical speed) Length of time of test: 363 seconds Average torque reading: 1,056 in-lbs Mill HP = (1,056 in-lbs / 12 in./ft) x (35.2 rpm
The ball mill is a tumbling mill that uses steel balls as the grinding media. The length of the cylindrical shell is usually 1–1.5 times the shell diameter (Figure 8.11 ). The feed can be dry, with less than 3% moisture to minimize ball coating, or slurry containing 20–40% water by weight.
The feed to the cyclone contains 36% solids by weight. It is found that 250 µm size in the rod mill discharge, ball mill discharge and cyclone feed is 27%, 5%, and 14% respectively. Determine the volumetric flow rate of feed (solid+ water) to the cyclone.
Suppose we get 55% of the original feed in the underflow and 45% in the overflow. "The circulating load ratio is necessary to determine the capacity of the ball mill initially. Once the ball mill is installed, you cannot change its capacity" The underflow is circulated into the ball mill as shown in the figure
حقوق النشر © 2024.Artom كل الحقوق محفوظة.خريطة الموقع