End mill design and machining via cutting simulation ...
The main idea of the process is to use the cutting simulation method to obtain the machined shape of an end mill by using Boolean operations between a given grinding wheel and a cylindrical workpiece (raw stock). The major design parameters of a cutter, such as rake angle and inner radius, can be verified by interrogating the section profile of ...
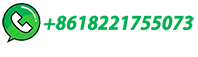