Enhance Production Monitoring With United Grinding's New ...
The C.O.R.E. panel has virtually no keys, and there is a rotary switch for feed rate override, enabling the axes to be regulated with a simple turn. United Grinding designed the new access system to have individual user profiles automatically loaded, and it works via a personalized radio-frequency identification (RFID) chip.
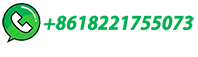