What is Cold Rolling? (with picture)
Cold rolling can be used to change the gauge of steel sheet metal. Cold rolling is a process used in manufacturing and finishing environments to change the thickness, or gauge, of metals or glass. Used mostly in steel mills, cold rolling …
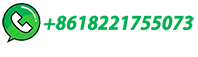