Vibration Characteristics of Rolling Mill System under ...
In order to simplify the research, taking into account the symmetry of the structure of the four-roller mill, only the upper roll of rolling mill system is analyzed. The vibration model of rolling mill system with nonlinear spring force and friction force constraints is established, and the diagram is shown in Figure 2.
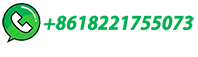