A Novel Approach to Improving the Efficiency of a Minimum ...
Abstract The potentialities concerning the combination of a cold-air minimum quantity lubrication technique (CAMQL) with a system for grinding-wheel cleaning by an air jet (WCJ) while grinding a heat-resistant nickel alloy are studied. The results of experimental studies show that, using the CAMQL + WCJ technique, the cutting force components are significantly …
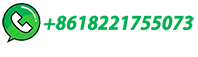