Aluminium | PyroData
Another source of usable aluminium powder is to burn tetra-paks, and then powder the resultant aluminium residue in a ball mill. Aluminium powder can also be found inside an Etch A Sketch. In Boating stores, it can be found as a two component epoxy for protection of boat hulls against UV radiation, mesh size is questionable.
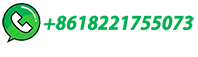