Grinding Parameters | SpringerLink
The grinding parameters depend on the actuated and system variables and allow a good correlation to the process forces, process temperatures, surface roughness, and grinding tool wear. The most important grinding parameters, that are described here, are the material removal rate Q w, the material removal rate per unit active grinding wheel ...
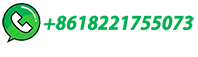