Superior Mechanical Performance of Inductively Sintered …
Next, all routes pass through stage 2, which can be called the high-speed ball milling stage. In this stage, the ball-powder-ball collisions are increased, inducing high compressive force, which...
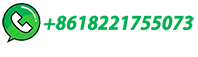