Attritor Ball Mill - Superfine Grinding Equipment with ...
Attritor ball mill is a kind of ultrafine grinding equipment with high output and energy saving.. With the development of science and technology, there are more and more applications of ultra-fine powders in industry. From ultra-fine grinding of metal and non-metal raw materials to deep processing of new composite materials, dozens of minerals are processed.
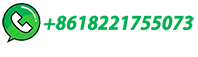