GRINDING MACHINES - Carnegie Mellon University
Grinding wheels come in many different sizes, shapes, and abrasives (Figure 5-7). Some of the various types are listed below. Straight Straight wheels, numbers 1, 5, and 7, are commonly applied to internal, cylindrical, horizontal spindle, surface, tool, and offhand grinding and snagging. The recesses in type
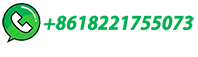