Coal Combustion - an overview | ScienceDirect Topics
Paul Breeze, in Coal-Fired Generation, 2015. Coal combustion is a dirty process, releasing a range of pollutants including sulphur dioxide, nitrogen oxides, carbon dioxide, volatile organic compounds, ash and a range of heavy metals. If these are not controlled they can enter the atmosphere, causing damage to the environment and to human health. Air quality standards …
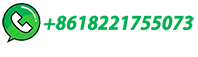