Glossary of Steel Industry Terms - American Iron and Steel ...
Steel – from Merriam-Webster Online. Pronunciation: stēl Function: noun Etymology: Middle English stele, from Old English style, stEle; akin to Old High German stahalsteel and perhaps to Sanskrit stakati he resists commercial iron that contains carbon in any amount up to about 1.7 percent as an essential alloying constituent, is malleable when under suitable conditions, and …
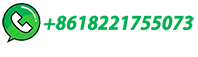