Pulverizer / Mill Upgrades » Babcock & Wilcox
Pulverizer / Mill Upgrades. A wide range of modifications and upgrades are available for your B&W Roll Wheel™ roller-type or E/EL ball-and-race pulverizers. These new components and technologies can be retrofitted onto existing pulverizers to provide you with the latest designs and operating benefits which can increase availability and ...
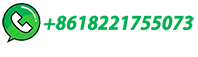