Continuous Generating Gear Grinding | Gear Solutions ...
O
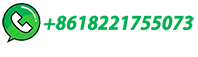
At its basic level, a grinding wheel is used to remove stock or material. But did you know there are several types available, all with different benefits? On...
The invention relates to a grinding machine for grinding of a gear or of a gear-like workpiece, which has a grinding worm ( 1 ) with a tooth-shaped profile ( 2 ), which consists at least partly from a dressable abrasive material and which is arranged rotatably on a grinding spindle, so that it can rotate around an axis of rotation (C) during grinding and a dressing device ( 3 ), with …
Threaded gear grinding In threaded gear grinding a number of motions occur simultaneously. The worm grinding wheel rotates on its axis while meshing with the gear workpiece which is rotating on its axis. The radial infeed to engage the gear being ground with the wheel is in the x direction. The infeed across the thickness of the gear is up and
At Gear Motions, gear grinding isn't just a capability – it's our specialty. It all began in 1969, with the purchase of our first gear grinding machine. Today, over 50 years later, Gear Motions is one of the premier precision gear manufacturing companies in the United States, thanks to a series of acquisitions, equipment investments and ...
GEAR GRINDING Grinding wheels are used to correct or modify the profile of gear teeth after heat treatment. The machine and gear type determine the shape of the grinding wheel. Continuous gear generation, profile grinding, bevel gear grinding, and power honing are the most common grinding processes in gear grinding.
Gear profile grinding Abrasive process of existing teeth sharpened with tools shaped like the tooth profile. The process Before grinding can be carried out, most of gear profile material has to be removed by gear forming method as this method only hone the teeth surface.
Gear Motions is a leading gear manufacturer specializing in supplying custom cut and ground gears for OEMs all around the world. Whether we're manufacturing your gear complete from start to finish or working from your blanks, our wide range of precision gear manufacturing capabilities and services deliver quality gears to meet almost any application – and the most demanding …
Gear Grinding ECONOMICAL SOLUTIONS FOR PRECISION GEAR GRINDING. Starting in 2007 Riverside Spline & Gear started construction of our new 10,000 sq. ft. Gear Grinding Center. Our first acquisition was the new 2007 Hofler 900 …
Gears are intentionally ground to remove unwanted material. Gear grinding is the name of a specific gear creation technique. Grinding involves the removal of unwanted materials through an abrasion process. Grinding is typically the last step in the gear creation process; other techniques have removed the majority of the material first.
What Material are Gears Made of? Generally, the gears are made of metal, plastic, and wood, the gear material should have the high tensile strength to prevent failure against static loads, high endurance strength to withstand dynamic loads, low coefficient of friction and good manufacturability.
The grinding of gears with dish wheels (Maad type grinding machines) is widely viewed as the most precise method of gear grinding because of the very short and simple kinematic links between the gear and the tool, and also because the cutting edges of …
Threaded gear grinding In threaded gear grinding a number of motions occur simultaneously. The worm grinding wheel rotates on its axis while mesh ing with the gear workpiece which is rotating on its axis. The radial infeed to engage the gear being ground with the wheel is in the x direction. The infeed across the thickness of the gear
Optimized gear manufacturing. The purpose of production activity is to create added value. This also applies to gear manufacturing, and added value creation is conducted through production control for the purpose of achieving QCD (quality, cost, volume and deadline), including everything from the procurement of raw materials such as round bars for cylindrical gears …
Grinding is a subset of cutting, as grinding is a true metal-cutting process. Each grain of abrasive functions as a microscopic single-point cutting edge (although of high negative rake angle ), and shears a tiny chip that is analogous to what would conventionally be called a "cut" chip (turning, milling, drilling, tapping, etc.).
facilitate the grinding of threads an gear teeth. Type 5. It is used for surface grinding, i.e. production of flat surfaces. Grinding takes place with the help of face of the wheel. ... These cannot be used for grinding of hard material and at faster speed. Emery is a natural aluminium oxide containing 55 to 65% alumina, rest are iron oxide and ...
Ball Mill. We bring forth a highly advanced Ball Mill, specifically engineered for both wet as well as dry cement grinding applications. Classified depending on the circuit design, bearing, grinding type and drive, the selection is made on the basis of the product fineness, quality, and nature of raw material, site conditions and specific requirements.
Grinding – Ex. 1-1 • You are grinding a steel, which has a specific grinding energy (u) of 35 W-s/mm3. • The grinding wheel rotates at 3600 rpm, has a diameter (D) of 150 mm, thickness (b) of 25 mm, and (c) 5 grains per mm2. The motor has a power of 2 kW. • The work piece moves (v) at 1.5 m/min. The chip thickness ratio (r) is 10.
The RZ 410 gear grinding machine combines universality, high precision and robust material removal rates. This machine represents state-of-the-art gear grinding technologies. As the grinding oil flow is completely separated from the machine bed, it …
There is a limit to grinding procedures and that is to ferrous material. Hard metals can be grind in an efficient and better way than the soft ones. In case of worm or helical gears, grinding may not be the ideal solution. This is due to the reason that it often involves deviations in terms of removal and profile.
Mechanical effects and proper grinding result in a compressive residual stress at the surface. This is beneficial for fatigue. Thermal effect produces the opposite effect, with a residual tensile field at the surface. As the part is locally heated, the surface layer expands, but it is constrained by the lower undisturbed material.
grinding hard materials or when the contact surface of the grinding wheel is small. The surface smoothness of the ground part depends not only on the grain size of the grinding wheel. The sharpness of the wheel, the bonding material used and the hardness of the wheel also play a considerable part in
Twitter https://twitter/BemoGuinness Instagram https:// TikTok https://@bemoguinness Website ht...
In soft gear process dynamic, the gear teeth are generated by gear hobbing or shaping depending on the component design constraints. Soft finishing of gear teeth is carried out by gear shaving, rolling or grinding to attain the gear quality grade. Even after the heat treatment
Project Shafts are mechanical parts that transmit motion, torque, or bending moments. Generally round metal rods, each segment can have different diameters. Motor shaft machining, stainless steel shaft machining, long shaft parts, precision shaft machining, small shaft machining, gear shaft machining, step shaft machining. Technology The product structure of the shaft is different.
-Gear Tools 11 CBN grinding tools are available as grinding worms and as profile discs with a galvanic CBN coating. The coating is cus-tomised for the specific machining requirements. The tools are primarily used for grinding involute gears with the highest possible quality requirements in mass production.
The process of grinding is the operation of removing excess material from metal parts by a grinding wheel made of hard abrasives. The following operations are generally performed in a grinding machine. 1. Cylindrical grinding 2. Taper grinding 3. Gear grinding 4. Thread grinding 4.5.1 Cylindrical grinding
Principles of Grinding. In all forms of grinding, three different interactions occur between the abrasive and the machined material. Cutting occurs where the abrasive grain is sufficiently exposed to penetrate the workpiece material and curl a chip, and sufficient clearance exists between the grain, bond and workpiece to flush the chip with coolant or throw it away by …
Gear Grinding Usually, gear grinding is performed after a gear has been cut and heat-treated to a high hardness Grinding is necessary for parts above 350 HB (38 HRC), where cutting becomes very difficult. Teeth made by grinding are usually those of fine pitch, where the amount of metal removed is very small. In addition, grinding of gears ...
Public research pertaining to the continuous generating gear grinding has been primarily focused on the processing of the tooth flank. Although profile grinding of the tooth root fillet can increase the gear lifetime up to 30% [6], so far, continuous generating grinding has been applied to it rather infrequently.
حقوق النشر © 2024.Artom كل الحقوق محفوظة.خريطة الموقع