(PDF) An analysis of cutting force and surface finish in ...
Braghini and Coelho [7] tested CBN to ols to face mill AISI D6 steel at 58HRC, removing. An analysis of cutting force and surface finish in surface grinding of …
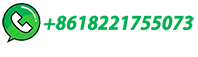
Braghini and Coelho [7] tested CBN to ols to face mill AISI D6 steel at 58HRC, removing. An analysis of cutting force and surface finish in surface grinding of …
Start by rough grinding with a pneumatic grinder with 36 to 80 grit discs. Finish grind with a pneumatic drum with a 40 to 220 grit abrasive belt. Then, work all surfaces with an extended pneumatic straight grinder and 60 to 240 grit fiber brushes. Finishing discs of synthetic fiber, grit and resin will eliminate welding discoloration.
Pinch grinding is a variation of peel grinding, which refers to high-speed cylindrical grinding of rotating blanks. In pinch grinding, however, the blank simultaneously passes through two opposing wheels: a roughing wheel and a …
Threaded grinding wheels enable continuous generation grinding, in which a number of motions occur simultaneously. The worm grinding wheel rotates on its axis while meshing with the gear workpiece which rotates on its axis. 3M™ …
By gripping the component in the gripper, either one of the two variable-speed finishing/grinding heads can be used. The first head, which is a stacked head, has a 40-HP lower spindle. This powerful motor can be used to drive large superabrasive and diamond wheels, as well as bonded wheels and large cutoff wheels (where 2 HP per inch of ...
The EDG3 is ANCA's new highly capable, low-cost solution for PCD, carbide (HM) and HSS tool manufacture and resharpening. Optimised for micro to large PCD drills, endmills and profile tools, the ANCA EDG3 is a highly versatile platform with an integrated direct-driven dual erosion and grinding spindle, allowing for supreme flexibility.
Fine grinding was suggested to improve the reactivity of blended cement constituents [10] [11][12]. Fine grinding leads to the generation of a larger …
Fine Grinding (flat parts – single or double-side) is the abrasive machining process for removing material using a bonded Superabrasive wheel at low speed with a liquid to keep the part cool. The fixed grain of a geometrically indefinable cutting shape acts like a plow (fig. 3) and material is removed by micro-grooving /-cutting (fig. 4).
Chelsea managed to grind out win over Leeds like true title hopefuls should. Chelsea know it will take a hell of a lot to finish ahead of both Manchester City and Liverpool in the final Premier ...
A finishing machine for internal spline tooth surfaces which comprises a holding device for holding a work having the internal spline tooth surfaces, a grinding stone having a plurality of tooth portions for simultaneously processing a plurality of tooth portions in the work, and a vibrating device for vibrating the grinding stone with a high speed in the axial direction of the …
Here are some grinding occurrences that will thwart superfinishing consistency: Too Smooth A Finish. Ironically, one of the most common of all grinding problems in relation to superfinishing is too smooth a finish. It is still not widely understood that too smooth a finish from the grinding operation is a negative factor.
Continuous Generating Grinding of Gears Only grinding can simultaneously deliver high surface finish and high precision geometry. Grinding is a metal cutting process that, due to innumerable cutting edges and high operating speed, can simultaneously deliver high material removal rate, superior surface finish and very precise geometry.
In this paper, an innovative shape adaptive grinding (SAG) tool is introduced that allows finishing of CVD silicon carbide with roughness below 0.4 nm Ra and high removal rates up-to 100 mm3/min ...
The grinding wheels are preferably formed each of two cylinders inserted the one in degrees of coarseness, so that the finish grinding of the work (coarse and fine) can be effected at one operation. An embodiment of the invention is illustrated by way of example in the accompanyirig drawings in which Q g Fig. 1. is a part topplan view of the ...
The finish grinding of the main and pin bearings takes place in OP 90 on a second PMD 2. MACHINING A VARIETY OF CRANKSHAFTS FROM A TWOCYLINDER SHAFT TO A V8 SHAFT ++ 30 kW (40 hp) motor spindles ...
Bahmueller's solution for this workpiece is centered around a special workholding, called mid-clamping, that chucks the part in the middle, allowing operators to grind the exposed sides of the workpiece simultaneously using two independent tools. The first operation is the I.D. grinding of multiple diameters in combination with face grinding.
Contact. Address: PFERD INC. 9201 W. Heather Ave. Milwaukee, WI 53224 Telephone: +1 (800) 342-9015 Fax: +1 (262) 255–2840 E-mail: sales@pferdusa
Striking a balance between strength and finesse, 3M offers abrasives designed to smooth metal surfaces while keeping part geometry intact and helping you get the finish you need. Grinding 3M offers a range of products to remove metal and welds, and shape parts to …
Product description. Color: Natural. The Magic Flight finishing grinder is made from the same beautiful sustainable woods that are used in the other hand-made Magic Flight products. The grinder comes in your choice of maple, walnut or cherry woods. This new grinder creates the type of micro-fine grind ideal for use in the launch box device.
1. Introduction. With the rapid development of abrasive belt processing in the past decade, belt grinding and finishing technologies have increasingly developed in the modern manufacturing industry [,, ].Particularly, combined with the multi-axis CNC [] and intelligent robot [], belt grinding can perform more complex and precise machining tasks without being limited to the traditional …
The grinding process is characterized by a large number of undefined cutting edges that are simultaneously in contact with the workpiece to achieve a fine surface finish and a high geometrical accuracy. To enable an efficient grinding process, the application of cutting fluids is an indispensable factor. This investigation shows that—depending on the cutting fluid …
The optimized grinding parameters by the improved FA could realize the achievement of all process quality objectives simultaneously with the grinding efficiency increased by 32.4%. Yildiz presented an improved DE algorithm to optimize turning process. 20 The minimized produce cost was the optimization objective.
Finishing process is conducted by slow speed grinding disc (wheel), at the same time applying water. So, the operator can apply water and grind concrete Simultaneously. The water and the rubbing action, brings up a cement paste which makes concrete very smooth, plaster-like surface.
From tempered steel to shiny blade, grinding stainless in my sub-freezing shed. …
Ultrasonic machining (UM) of ceramics is the machining method using the action of a slurry containing abrasive particles flowing between the workpiece and a tool vibrating at an ultrasonic frequency. The vibration frequency is 19 ~ 25 kHz. The amplitude of vibration 0.0005 - 0.002" (13 – 50 μm). During the operation the tool is pressed to the workpiece at a constant load.
The can grind and finish simultaneously. Just apply heavier pressure for aggressive grinding and lighter pressure for a finer finish. The Kim-Flex line provides fast cutting action with flexible discs that conform to curved, contoured and irregular surfaces. They come in a variety of grits, diameters and densities so you can get the right ...
Method of grinding a concentrically clamped crankshaft, a crankshaft grinding machine for carrying out the method, and a crankshaft of high-alloy steel or cast material. The method provides for pin journals and main journals of the crankshaft to be ground in one set-up such that first, at least the main journals are rough-ground and then the pin journals are finish-ground …
The present invention relates to a method of grinding a concentrically clamped crankshaft, a crankshaft grinding machine for carrying out the method, and a crankshaft of high-alloy steel or cast material. The method provides for pin journals and main journals of the crankshaft to be ground in one set-up such that first, at least the main journals are rough-ground and then the …
600408680 vs Cordless Finish Nailer: High grain concentration for violent grinding action and smoother running wheels 20v Max. For low angle & vertical grinding 600408680. Silicon carbide grain for long wheel life in all masonry materials. 600408680 Cutter W:
حقوق النشر © 2024.Artom كل الحقوق محفوظة.خريطة الموقع