Wheel Dressers and Dressing Tools Specifications ...
Diamond is used for dressing bonded abrasive wheels and products as well as grinding nonferrous metals, ceramics, glass, stone, and building materials. Aluminum Oxide Aluminum oxide is the most common industrial mineral in use today.
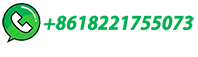