Products and processing | Ferrexpo Plc
Ferrexpo primarily produces high grade iron ore pellets that contain either 65% or 67% iron which are the highest grades in the global pellet industry. Production of our highest grade (67% Fe) direct reduction pellets commenced in 2020, and through investment in our operations, we are delivering volume and quality enhancements throughout our production process.
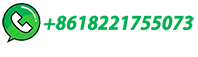