cement mill power calculation - Mine Equipments
Cement industry, power plants - Klingelnberg Employed primarily in the cement industry and in coal-fired power plants, vertical mills are used to grind lime stone, clinker brick, and coal. ... From the initial calculation and design of the gear sets all the way to practical simulations and ...
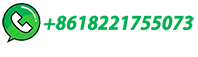