The composition and characteristics of Great Wall Cement ...
Cement Production Line mainly contains material crushing, homogenizing, preheating decomposition, calcined cement clinker,cement grinding,finished product packing and so on,the composition of Cement Production Line mainly contains Rotary Kiln,Cement Mill,Cyclone Preheater,Cooler and so on.On Cement Production Line,the correct Cement Mill …
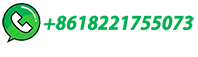