Cement manufacturing - components of a cement plant
Cement manufacturing: components of a cement plant. This page and the linked pages below summarize the cement manufacturing process from the perspective of the individual components of a cement plant - the kiln, the cement mill etc.. For information on materials, including reactions in the kiln, see the ' Clinker ' pages.
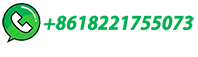