End Mill Grinder - Toolots
3. Determine the cutting face diameter of the End mill and choose proper grinding wheel. ① For grinding Shelf (I) and Shelf (II), there are three different sizes of grinding wheel. Grinding Wheel A is for grinding the diameter from Φ3.0 mm - Φ5.0 mm. Grinding Wheel B is for grinding the diameter from Φ5.1 mm - Φ8.0 mm.
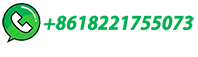