Ball Mill Operating Speed - Mechanical Operations Solved ...
The critical speed of ball mill is given by, where R = radius of ball mill; r = radius of ball. For R = 1000 mm and r = 50 mm, n c = 30.7 rpm. But the mill is operated at a speed of 15 rpm. Therefore, the mill is operated at 100 x 15/30.7 = 48.86 % of critical speed. If 100 mm dia balls are replaced by 50 mm dia balls, and the other conditions ...
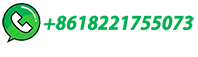