The Importance of Abrasive Grinding Wheel Hardness Control ...
The Importance of Abrasive Grinding Wheel Hardness Control of Production Grinding Operations for the Productivity C. P. Bhateja (2) - Submitted by R. P. Lindsay (3) - s Umn~ The productivity of certain types of grinding o?erations in industry is very sensitive to the variations in abrasive grinding wheel hardness.
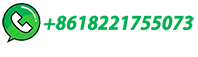