SAG mill increases productivity, reduces unscheduled ...
The application. Industrial milling of mined ore – from large rocks and boulders to fine particles – is a demanding process. Massive semiautogenous mills – commonly known as SAG mills – use milling balls, as well as the weight of the ore itself, to break down the ore into smaller particles – a process known as comminution.
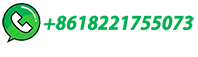