Grinding - SlideShare
Grinding 1. Grinding and Grinding Machine 2. Grinding: Grinding is a process of removing material by abrasive action of a revolving wheel on the surface of a work-piece in order to bring it to required shape and size The wheel used for performing the grinding operation is known as grinding wheel It consists of sharp crystal called abrasive held together by a …
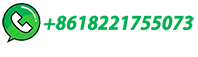